What is Die Casting? A Comprehensive Guide to the Process, Materials, Applications, and Costs
Table of Contents
- The Mechanism and History of Die Casting
- Different Types of Die Casting Processes
- Detailed Steps in the Die Casting Process
- Die Casting Alloy Selection
- Surface Treatment Options
- Applications of Die-Cast Parts
- Advantages and Disadvantages of Die Casting
- Factors Affecting Die Casting Costs
- Recommended Products
- Frequently Asked Questions
The Mechanism and History of Die Casting
Die casting technology dates back to the early 19th century. In 1849, Sturges designed the first manual die-casting machine, laying the groundwork for the die casting industry. With industrialization, especially after Otto Mergenthaler’s invention of the typesetting machine in 1855, the efficiency of die casting improved significantly. By the late 19th century, aluminum gradually replaced tin and lead as the primary material used in die casting, and the advent of high-pressure die casting greatly improved production efficiency and part quality.
Different Types of Die Casting Processes
Hot Chamber Die Casting
Hot chamber die casting is suitable for processing low-melting-point metals such as zinc, tin, lead, and magnesium. In this process, the molten metal is injected into the mold under high pressure through a hydraulic system. Since the hydraulic system remains in direct contact with the molten metal, this method is ideal for metals with low melting points. The hot chamber die casting process is ideal for producing small parts in high volumes.
Cold Chamber Die Casting
Cold chamber die casting is used for high-melting-point metals, particularly aluminum alloys. Unlike the hot chamber process, the molten metal is poured manually or automatically into a cold chamber before being injected into the mold at high pressure. This process is best suited for metals like aluminum that require higher temperatures for melting.
Detailed Steps in the Die Casting Process
Clamping Process
Before injection, the mold must be cleaned and lubricated to ensure it is free from impurities. High-pressure clamping is used to tightly close the mold, preparing it for injection.
Injection Stage
During this stage, the molten metal is rapidly injected into the mold under high pressure. The speed and pressure at which the metal is injected play a crucial role in the quality and precision of the final part.
Cooling and Ejection
Once the metal solidifies inside the mold, the mold is released, and the ejection mechanism pushes the solidified part out of the mold.
Finishing Steps
Excess material such as gates and runners is removed, and the recovered metal can be reused for future casts.
Die Casting Alloy Selection
The Use of Aluminum Alloys
Aluminum alloys are commonly used in die casting due to their excellent strength-to-weight ratio, corrosion resistance, and thermal conductivity. Common aluminum alloys, such as 380.0, are widely used in automotive and electronic industries.
Characteristics of Zinc Alloys
Zinc alloys are known for their superior mechanical strength and durability, combined with cost-effective production. Typical zinc alloys include Zamak #2, #3, and ZA8. These alloys are commonly used in the automotive, electronics, and small mechanical components industries.
Magnesium Alloys and Other Alloys
Magnesium alloys are valued for their low density and high strength, making them ideal for aerospace and automotive applications. Other alloys, such as bronze and tin, are used in specialized applications where corrosion resistance and aesthetics are essential.
Surface Treatment Options
Common Surface Treatment Techniques
Surface treatments play a crucial role in improving the aesthetics and durability of die-cast parts. Common methods include painting, powder coating, and electroplating. Powder coating is particularly popular for its excellent thickness control and uniformity.
Ceramic Coating and Antique Replication
Ceramic coatings provide corrosion resistance and durability similar to anodizing. Antique replication uses electroplating and chemical treatments to give zinc die-cast parts an antique appearance, often used in high-end consumer goods.
Applications of Die-Cast Parts
Consumer Goods and Industrial Applications
Die casting is widely used in the production of everyday and industrial products, such as faucets, compressor pistons, and heat exchangers. The precision and efficiency of the process make it ideal for both consumer and industrial parts.
Automotive and Aerospace Applications
In the automotive industry, die casting is used to produce engine components, gears, and transmission parts. In aerospace, die casting is used to manufacture high-strength, lightweight metal parts that meet strict quality standards.
Advantages and Disadvantages of Die Casting
Advantages of Die Casting
Die casting offers several advantages, including the ability to produce complex shapes quickly and efficiently, as well as reducing labor costs. The process is well-suited for large-scale production, particularly when parts require high precision and dimensional accuracy.
Limitations of Die Casting
Despite its many benefits, die casting has some limitations. High mold costs and long production cycles can make it less suitable for low-volume production. Additionally, it is not ideal for high-melting-point metals or larger parts.
Factors Affecting Die Casting Costs
Material Selection and Production Costs
The choice of material has a significant impact on die casting costs. Aluminum, zinc, and other alloys vary in price, affecting the overall cost of production. Mold fabrication and maintenance costs are also important considerations.
Secondary and Finishing Operations Costs
Secondary operations, such as trimming and surface treatments, also contribute to the overall cost. Specialized techniques like electroplating add to the cost of production but offer enhanced durability and aesthetics.
Recommended Products
SquareBeam Elite
If you’re looking for efficient and high-quality lighting solutions, CAE Lighting’s SquareBeam Elite LED lighting products are an excellent choice. Featuring the latest LED technology, they offer superior brightness and energy efficiency, ideal for industrial environments and large-scale applications.
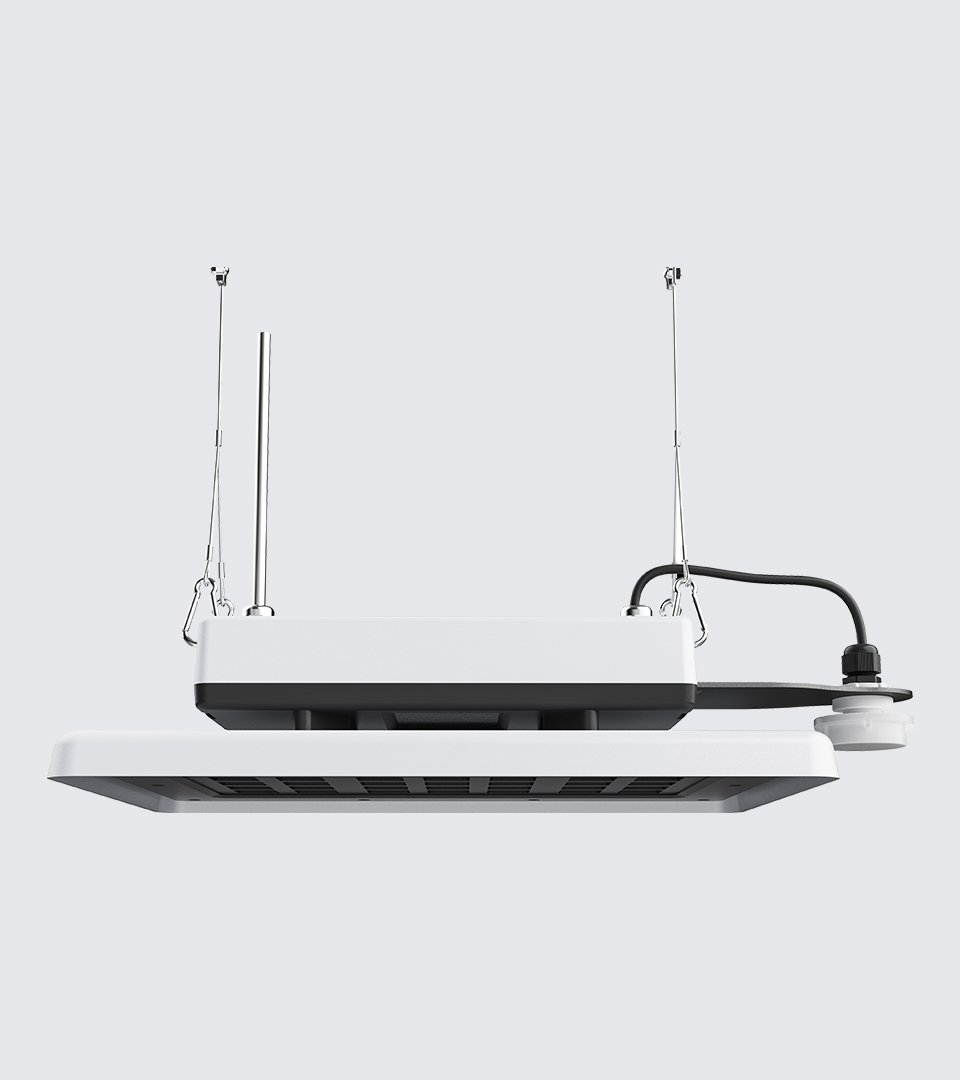
Budge High Bay Light
If you need affordable high-bay lighting for high-ceiling applications, the Budge High Bay Light is the perfect option. It offers outstanding durability and long-lasting performance, making it ideal for warehouses and industrial spaces.
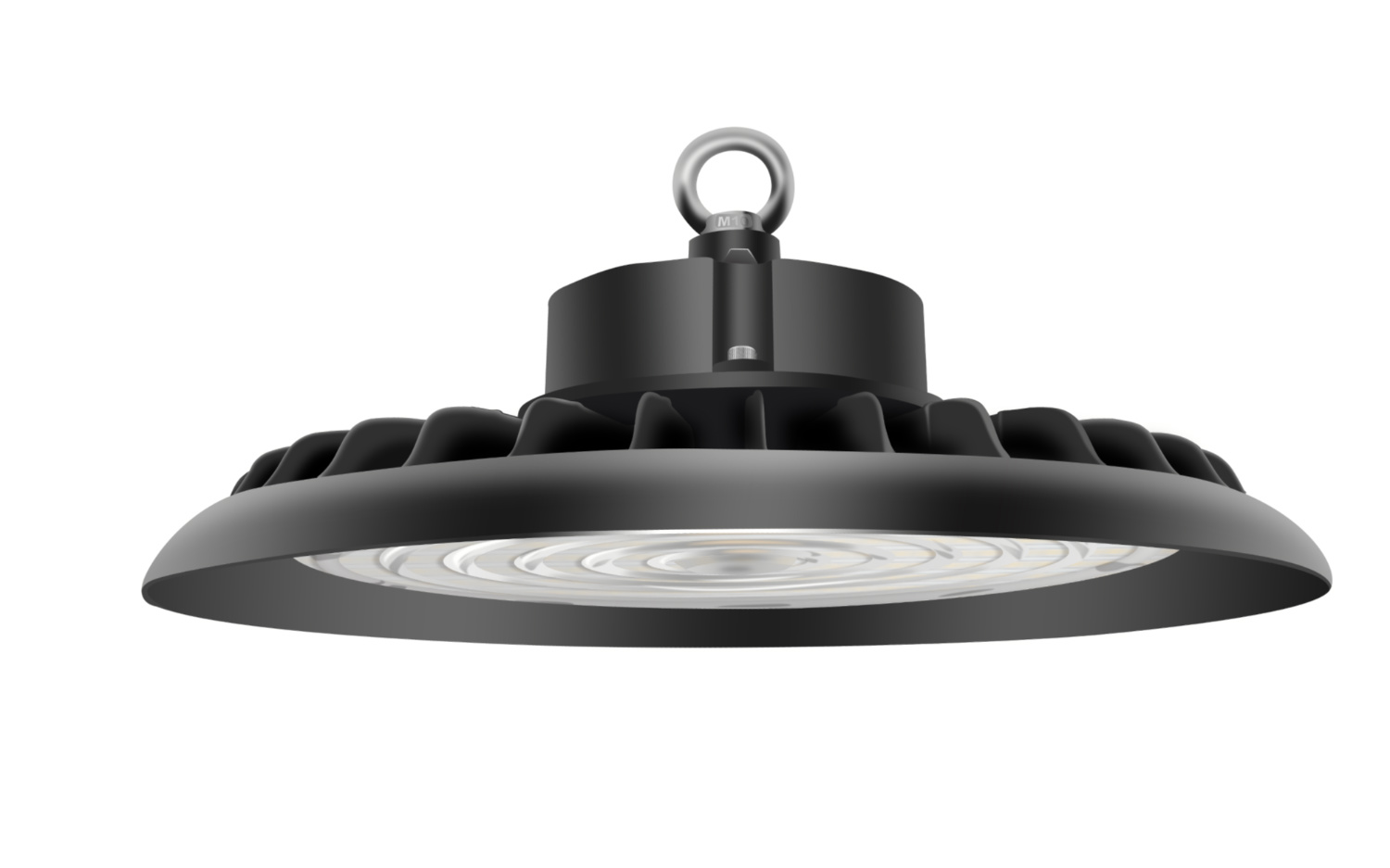
Frequently Asked Questions
Q1: What are the main benefits of die casting?
Die casting offers fast production cycles for complex shapes at low costs, making it highly popular across many industries.
Q2: What is the difference between hot chamber and cold chamber die casting?
Hot chamber die casting is used for low-melting-point metals, while cold chamber die casting is suited for metals with higher melting points, like aluminum.
Q3: Which alloy is best suited for die casting?
It depends on the application, but aluminum and zinc alloys are the most commonly used due to their excellent mechanical properties and cost-effectiveness.